Have you ever wondered how the intricate, sturdy metal parts in your car door or the solid-feeling handle on a cabinet are made? There’s a good chance they are products of zinc die casting. This process is a powerhouse in modern manufacturing, prized for its unique blend of strength, precision, and incredible production speed, making it an unsung hero in many industries—especially automotive.
Zinc die casting uses hot-chamber injection of molten zinc alloy into steel dies to produce strong, precise parts—often faster and cheaper than aluminum with superior surface finish and conductivity.
Let’s dive deeper. Together, we’ll explore the step-by-step process, compare the most popular alloys, uncover the material’s key benefits, see its real-world automotive applications, and find out how it stacks up against other casting methods.
- What Is Zinc Die Casting?
- How Zinc Die Casting Works: A 4-Step Process
- Zinc Alloys & Their Material Properties
- Why Zinc? The Big Benefits Compared to Aluminum
- Applications of Zinc Die Casting Across Industries
- Automotive Focus: Real-World Case Studies
- Pros & Cons of Zinc Die Casting: An At-a-Glance Table
- Choosing Zinc vs. Aluminum Die Casting: A Head-to-Head Battle
- Frequently Asked Questions (FAQs)
- Conclusion: Why Zinc Might Be Your Best Choice
- Crafting Excellence, Together
What Is Zinc Die Casting?
So, let’s get right to it. At its core, zinc die casting is a metal casting process where molten zinc alloy is forced into a reusable steel mold—called a die—under high pressure. The metal cools and solidifies, taking on the shape of the mold’s internal cavity. What truly sets zinc die casting apart is that it predominantly uses the hot-chamber method.
Imagine a furnace full of molten zinc alloy. In the hot-chamber process, the injection mechanism—a plunger system often called a “gooseneck”—is submerged directly within this molten metal bath. When a shot is fired, the plunger forces the liquid metal through the gooseneck and into the die. This is fundamentally different from the cold-chamber process used for metals with higher melting points like aluminum, where the molten metal is ladled into the injection system for each shot. Because the zinc is injected from a direct, internal source, the process is incredibly fast, efficient, and repeatable. I’ve seen this method dramatically slash production times for our clients.
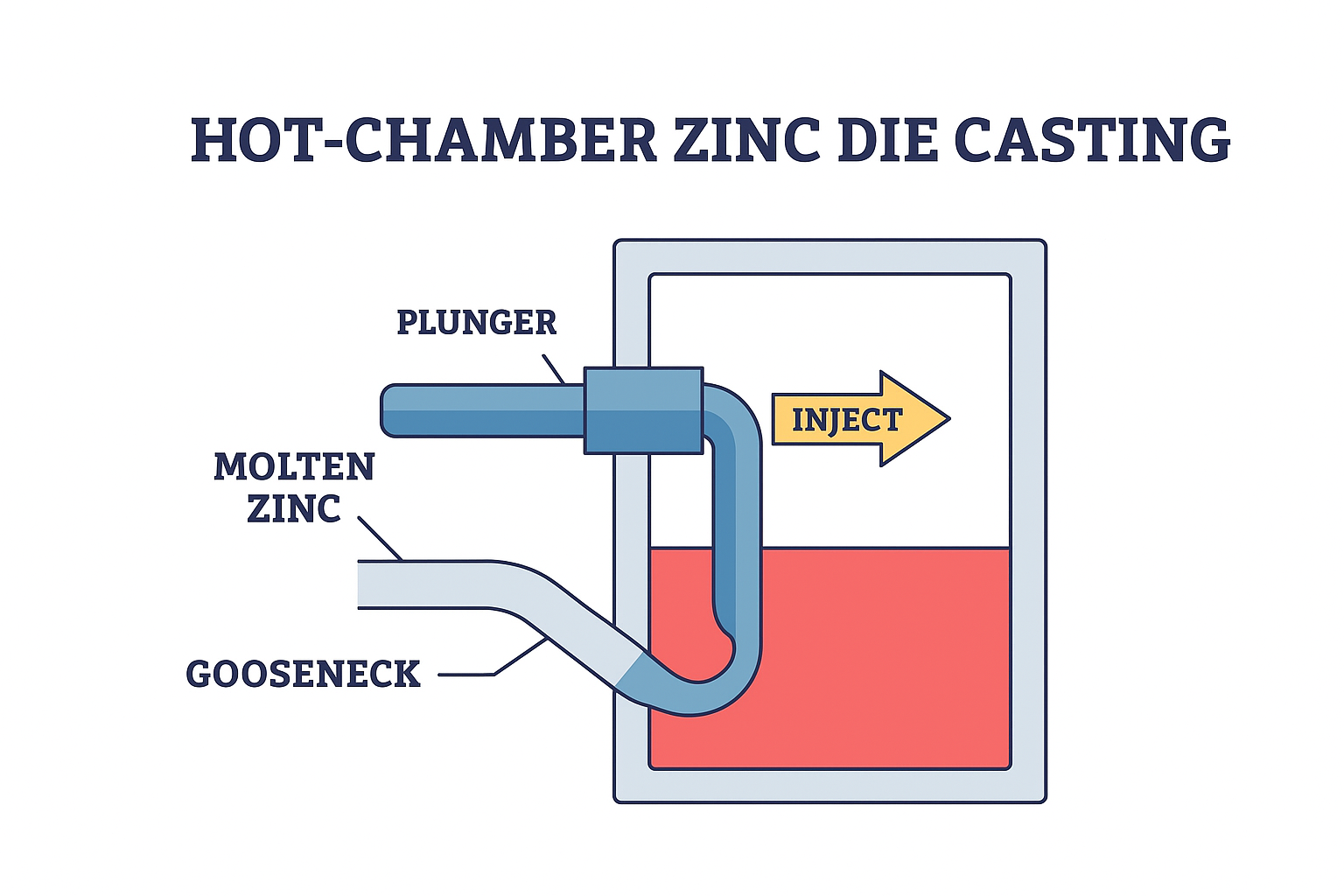
Common Zinc Alloy Types
Not all zinc is created equal. The specific properties of a finished part depend heavily on the alloy used. While there are many options, you’ll most often encounter two main families:
Zamak Alloys: This is the workhorse family of zinc alloys, with Zamak 3 being the most widely used die casting alloy in North America (Source: Eastern Alloys). It offers an excellent balance of physical and mechanical properties, superb castability, and a beautiful finishing surface. It’s the go-to choice for a vast range of applications.
ZA Alloys: The Zinc-Aluminum (ZA) alloys, like ZA-8, ZA-12, and ZA-27, contain a higher percentage of aluminum. This gives them enhanced strength, hardness, and wear resistance compared to the Zamak family. ZA-12, for example, is a great choice when you need a bit more strength than Zamak 3 can offer, but still want to use the die casting process.
How Zinc Die Casting Works: A 4-Step Process
I love the elegance of the die casting process because it’s a beautifully orchestrated sequence. While the machines are complex, the core process can be broken down into four main steps.
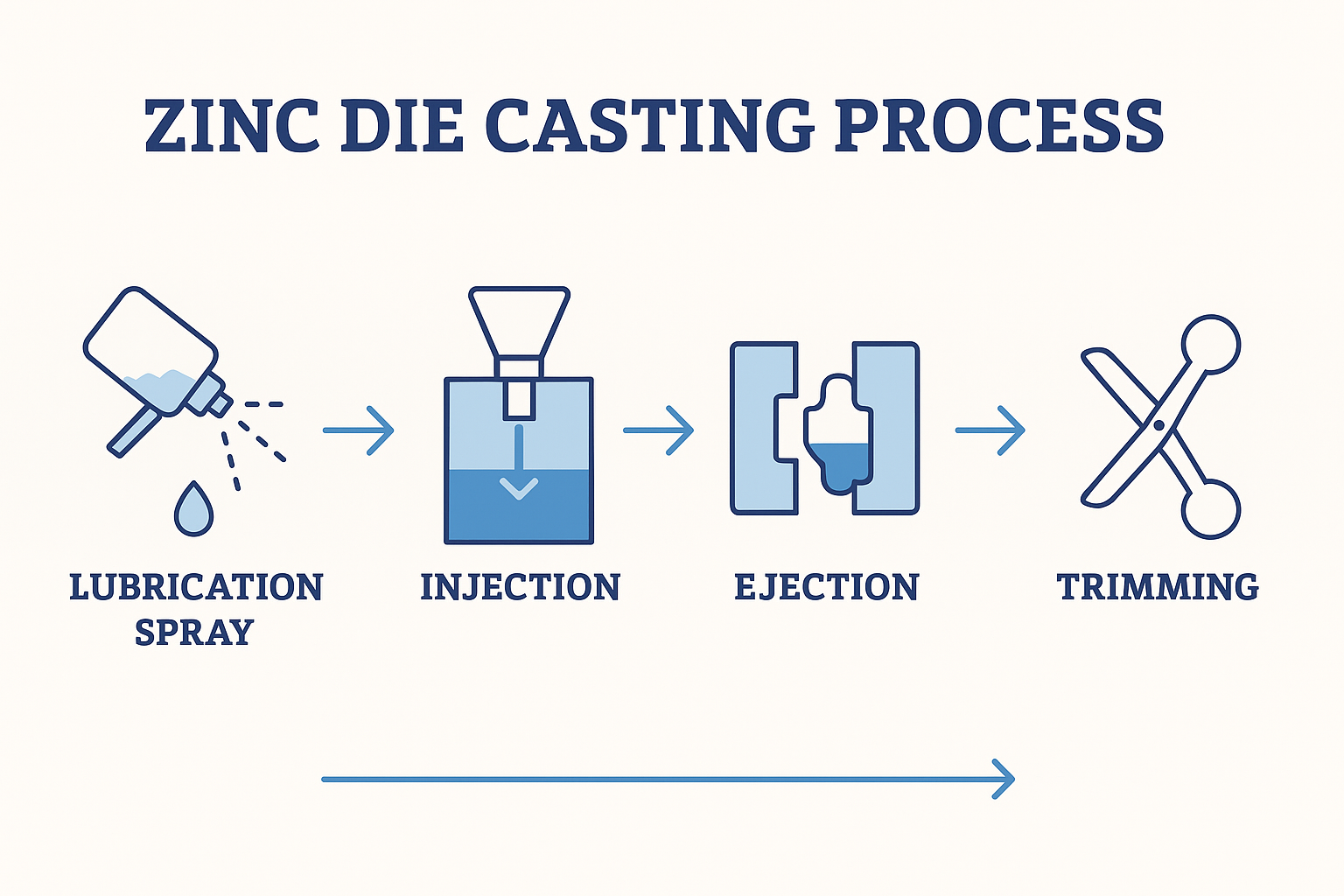
Step 1: Die Preparation and Lubrication
Before anything else, the two halves of the steel die must be prepared. They are cleaned of any debris from the previous shot and sprayed with a lubricant. This might sound minor, but it’s crucial. The lubricant helps control the die’s temperature and, more importantly, ensures that the solidified part can be easily ejected later. Think of it as greasing a baking pan before you pour in the cake batter.
Step 2: Molten Alloy Injection
This is where the magic happens. The two halves of the die are securely clamped together under immense force. The hot-chamber machine then injects the molten zinc alloy into the die cavity at high speed and pressure. This can happen in a fraction of a second—pressures can range from 1,500 to over 25,000 pounds per square inch (psi) (Source: NADCA). This intense pressure ensures the molten metal fills every tiny nook, cranny, and detail of the mold, creating a precise and net-shape part
Step 3: Cooling and Ejection
Once the die cavity is filled, the molten zinc cools down rapidly, solidifying into its final shape. The low melting point of zinc alloys really helps speed this part up. After a very short cooling period, the die halves are opened, and an ejection mechanism, typically a series of pins, pushes the solidified casting out of the mold.
Step 4: Trimming
The freshly ejected part isn’t quite finished yet. It will have some excess material, known as “flash,” where the two die halves met, as well as runners and gates (the channels the molten metal flowed through). This excess material is trimmed away, either manually or using an automated trim die. The great news is that all this trimmed zinc material is 100% recyclable and can be re-melted and used again, making the process very waste-efficient.
Zinc Alloys & Their Material Properties
Choosing the right alloy is like choosing the right ingredient for a recipe—it dictates the final outcome. The Zamak and ZA series offer a versatile toolbox for engineers.
The Zamak series (an acronym for Zinc, Aluminum, Magnesium, and Copper in German) is the industry standard for general-purpose die casting.
The ZA series, with its higher aluminum content, is specified when you need to push the boundaries of strength and wear resistance. For example, ZA-12 can be a fantastic bearing material because of its excellent hardness and wear characteristics.
Here’s a quick comparison of some popular choices to give you a clearer picture:
Alloy Type | Tensile Strength (MPa) | Melting Point (°C / °F) | Key Characteristics & Common Finish |
Zamak 3 | ~283 | ~387°C / 728°F | The de-facto standard; excellent stability, highly castable. Finishes beautifully with plating, painting, or powder coating. |
Zamak 5 | ~331 | ~386°C / 727°F | Slightly harder and stronger than Zamak 3 due to added copper, but a bit less ductile. |
ZA-8 | ~374 | ~385°C / 725°F | Highest strength of the hot-chamber ZA alloys. Can be easily plated and finished. |
ZA-12 | ~404 | ~404°C / 759°F | A good middle-ground; offers higher strength and better bearing properties. Often used in cold-chamber machines but can be hot-chamber cast. |
Why Zinc? The Big Benefits Compared to Aluminum
This is a question I get all the time. Aluminum die casting is incredibly popular, so why would you choose zinc? The answer comes down to a few game-changing advantages that zinc holds in specific situations.
Blazing Fast Cycle Speed
This is probably zinc’s biggest claim to fame. Thanks to its lower melting point and the efficiency of the hot-chamber process, zinc parts can be produced much, much faster than aluminum parts. We’re talking about cycle speeds that are 150% to 200% faster. For a high-volume production run, this is a massive advantage. If you need hundreds of thousands of identical parts, that speed translates directly into lower part costs and faster delivery.
Incredible Net-Shape Precision
Zinc alloys allow for casting parts with exceptionally tight tolerances and thin walls. It’s possible to achieve tolerances as tight as ±0.001 inches (±0.025 mm) directly from the die. This means the part comes out of the mold already in its final, or “net-shape,” form, often eliminating the need for expensive and time-consuming secondary machining operations. Zinc can also fill wall sections as thin as 0.025 inches (0.635 mm), which is difficult to achieve with other metals.
Superior Surface Finish
If you need a part with a pristine, smooth surface right out of the gate, zinc is your champion. Zinc castings naturally have an excellent surface finish, which is ideal for parts that will be visible to the consumer. This makes it a perfect substrate for a wide variety of finishes, from chrome plating and powder coating to simple painting, with minimal surface preparation required.
Natural Conductivity and Shielding
In our increasingly electronic world, this is a huge benefit. Zinc alloys are excellent electrical conductors and provide inherent EMI/RFI (Electromagnetic Interference/Radio-Frequency Interference) shielding. This is why you see it used so often for housings for electronic sensors and connectors, as it creates a natural protective metal case.
Excellent Wear Resistance and Bearing Properties
Certain zinc alloys, particularly the ZA series, are surprisingly tough and have excellent bearing and wear properties. They can often replace traditional bronze bushings in applications with high loads and slow speeds, offering a more cost-effective solution without sacrificing performance.
100% Recyclability
As I mentioned before, all the scrap material from zinc die casting—from runners to rejected parts—can be re-melted and reused. This commitment to sustainability is not just good for the planet; it’s also good for the bottom line, as it minimizes material waste.
Applications of Zinc Die Casting Across Industries
While our main focus here is automotive, zinc’s versatility makes it a popular choice across a huge range of sectors. You’ve almost certainly interacted with a zinc die-cast part today without even realizing it.
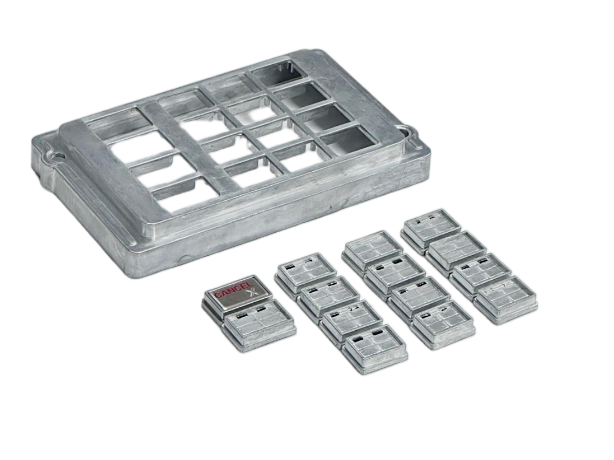
- Automotive: This is a massive market for zinc. It’s used for everything from safety-critical components like seat belt retractor gears to decorative parts like emblems and interior trim. We’ll explore this more in a moment.
- Electronics: Connectors, heat sinks, and housings for sensors all benefit from zinc’s precision and electrical properties.
- Hardware: Think about the handles and knobs on your kitchen cabinets, locksets on your doors, and faucet bodies in your bathroom. Many of these are zinc, chosen for their solid feel, durability, and excellent finish.
- Industrial: Fasteners, pulleys, gears, and various machine components are often made from zinc due to its strength and cost-effectiveness.
Automotive Focus: Real-World Case Studies
The automotive industry operates on razor-thin margins and demands absolute reliability. This is where zinc die casting truly shines. Let’s look at a few examples of how it’s used to make our vehicles safer and more functional.
Case Study 1: Seat Belt Gears and Pulleys
- The Part: The small, intricate gears and spools inside a seat belt retractor mechanism.
- The Challenge: These parts are absolutely critical for safety. They must be incredibly strong and dimensionally perfect to ensure the locking mechanism engages instantly during a collision. They also need to be produced in the millions with perfect consistency.
- Why Zinc Wins: The high tensile strength of zinc alloys provides the necessary durability. The net-shape precision of die casting ensures every single gear tooth is perfectly formed without the need for machining. Finally, the rapid cycle speed makes it economically feasible to produce these high-volume, life-saving components.The Part: The small, intricate gears and spools inside a seat belt retractor mechanism.
- The Challenge: These parts are absolutely critical for safety. They must be incredibly strong and dimensionally perfect to ensure the locking mechanism engages instantly during a collision. They also need to be produced in the millions with perfect consistency.
Case Study 2: Electronic Sensor Housings
- The Part: The protective casing for a parking sensor, ABS (Anti-lock Braking System) module, or other electronic control unit (ECU).
- The Challenge: These housings must protect sensitive electronics from vibration, moisture, and impact. Crucially, they also need to shield the electronics from electromagnetic interference (EMI) that could disrupt their function.
- Why Zinc Wins: Zinc’s inherent strength and corrosion resistance provide excellent physical protection. But the real star here is its natural EMI shielding capability. The cast metal housing forms a complete Faraday cage around the electronics, preventing interference without needing additional shielding materials, which simplifies design and lowers cost.
Case Study 3: Door Locks and Rear-View Mirror Bodies
The Part: The internal lock mechanism in a car door or the main body and stem of a rear-view mirror.
The Challenge: These are “touchpoint” components. They need to feel solid and high-quality to the consumer. They must also be durable enough to withstand thousands of use cycles and have a smooth surface for painting or chrome plating.
Why Zinc Wins: Zinc provides a satisfying density and weight, giving parts a “quality” feel that lighter materials can’t match. Its excellent surface finish straight from the die creates a perfect canvas for Class-A cosmetic finishes. The process’s ability to create complex internal features in a single step makes it ideal for intricate lock assemblies.
Pros & Cons of Zinc Die Casting: An At-a-Glance Table
No process is perfect for every single application. It’s all about trade-offs. Here’s a straightforward breakdown of where zinc die casting excels and where it has limitations.
Pros | Cons |
Extremely fast cycle speed, lowering part cost | Limited to metals with lower melting points |
High dimensional accuracy and stability | Less ideal for very large structural components |
Excellent surface finish for plating or painting | Initial die costs can be high (but offset by volume) |
Good conductivity, EMI shielding, and recyclability | Not suitable for parts exposed to high temperatures |
Choosing Zinc vs. Aluminum Die Casting: A Head-to-Head Battle
This is the final boss battle for many engineers. Both are fantastic processes, but they are suited for different jobs. Let’s put them side-by-side. My personal rule of thumb is: if you need massive volumes of small, intricate parts with a great finish, start with zinc. If you need a larger, lightweight structural part, look at aluminum.
Feature | Zinc Die Casting | Aluminum Die Casting |
Process | Hot-Chamber | Cold-Chamber |
Melting Point | Lower (~380°C / 716°F) | Higher (~660°C / 1220°F) |
Cycle Speed | Much Faster (up to 200% faster) | Slower |
Precision | Higher (tighter tolerances possible) | Good, but typically requires more machining |
Mold Life | Much Longer (often > 1 million shots) | Shorter (typically 100,000-150,000 shots) |
Part Cost | Lower for high volumes | Higher for high volumes, but can be cheaper for low volumes |
Weight | Denser / Heavier | Lighter |
Wall Thickness | Can produce thinner walls | Requires thicker walls |
Strength-to-Weight | Good | Excellent |
The most telling factor here is mold life. Because zinc has a much lower melting point and is less abrasive, the steel dies used in zinc casting last dramatically longer. A zinc die can often produce over a million parts, whereas an aluminum die might wear out after 150,000. This long-term tooling advantage is a major contributor to zinc’s lower piece-part price on high-volume runs.
Frequently Asked Questions (FAQs)
Absolutely. The alloys used in die casting are engineered for high performance. They possess the strength, toughness, and rigidity required for many demanding applications, including safety-critical parts like the seat belt components we discussed. Their long history of successful use in the automotive sector is a testament to their reliability.
Generally, no. Zinc alloys have a low melting point, so conventional heat treatment processes would damage or melt the part. Similarly, they are not typically joined by welding. Instead, parts are designed to be cast to their final net shape, and if assembly is needed, it’s done through mechanical means like staking, crimping, or using fasteners.
This is one of zinc’s superpowers. With careful die design and process control, it’s possible to cast walls as thin as 0.5 mm (about 0.020 inches). This allows for the creation of lightweight and highly detailed parts that would be impossible to produce with many other casting methods.
Yes, zinc alloy can tarnish over time, but the process is relatively slow and nuanced compared to other metals.
The process that causes tarnishing is a chemical reaction called oxidation. When the surface of the zinc alloy is exposed to oxygen and moisture, it forms a protective layer of zinc carbonate. In industrial settings, this dull layer is a desirable patina that shields the underlying metal from further corrosion.
However, in a decorative context, this patina is seen as tarnish. Instead of maintaining its bright, silvery sheen, a tarnished zinc alloy part will lose its luster and can take on a cloudy, milky-white, or grayish appearance.
Several factors can accelerate this process:
1. Humidity and Moisture: The primary catalyst for oxidation.
2. Air Pollutants: Chemicals like sulfur compounds react with the surface.
3. Acids and Salts: Contact with sweat, lotions, and perfumes will speed up tarnishing.
Most consumer-facing zinc alloy parts are protected with a coating—like chrome plating or a clear lacquer—which acts as a barrier to prevent tarnishing. For uncoated items, keeping them dry and away from chemicals is the best way to maintain their appearance.
Conclusion: Why Zinc Might Be Your Best Choice
So, what’s the big takeaway? Zinc die casting isn’t just an alternative to aluminum; it’s a first-class manufacturing process with its own powerful set of advantages.
When your project demands high volumes of complex, precise parts with a flawless surface finish, zinc should be at the top of your list. Its incredible speed, tight tolerances, and long tool life make it an economic and engineering champion for countless components in the automotive world and beyond.
Now I’d like to hear from you. Are you considering zinc for a project, or did one of its benefits surprise you? When you’re ready to take the next step, I encourage you to reach out to a manufacturing expert for a technical consultation or to request a quote.