WELCOME TO CASTMOLD
Aluminum & Zinc Alloy Die Casting — From Prototype to Production
Fast sampling & flexible MOQs, delivered in days.
HPDC + CNC finishing, precision from design to delivery.
ISO 9001:2015 Certified Factory
Our Manufacturing Capabilities
With in-house HPDC machines and a proven Yangtze River Delta supply chain, we achieve ±0.05mm precision in 0.6mm thin-wall casting. Supported by ISO 9001-certified quality control, we deliver rapid prototypes to full production , backed by 2M+ monthly capacity.
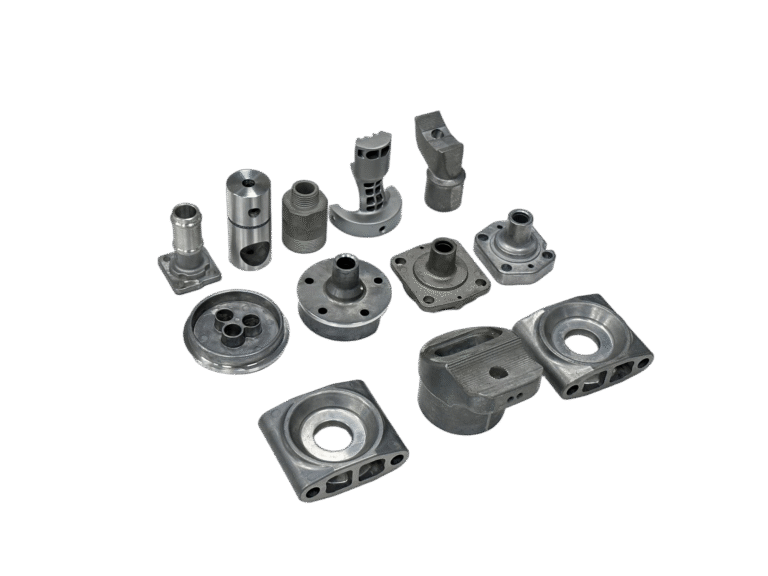
Aluminum Die Casting
High-precision aluminum die cast parts for complex, high-volume applications.
- Minimum batch: 500 pcs
- Minimum wall thickness: 0.5 mm
- Lead times from 15 days
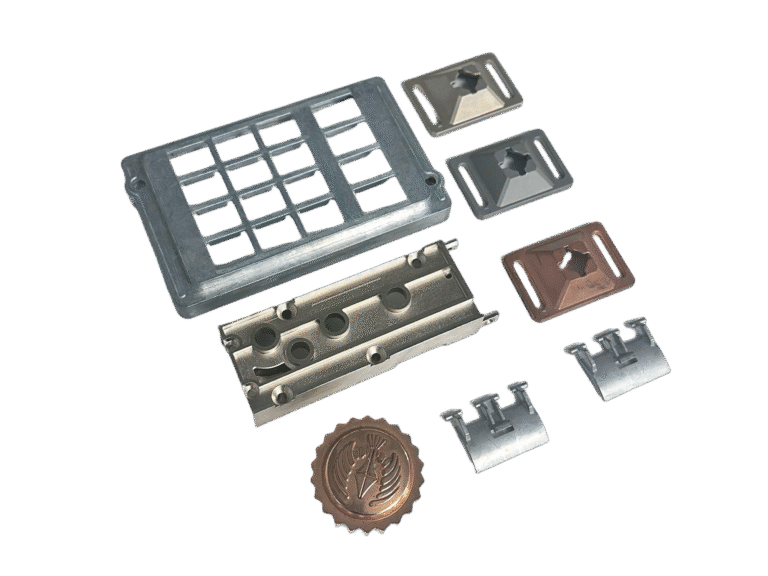
Zinc Die Casting
Choose from Zamak 2/3/5/7 alloys for tight-tolerance, small-part production.
- Minimum batch: 500 pcs
- Minimum wall thickness: 0.5 mm
- Lead times from 15 days
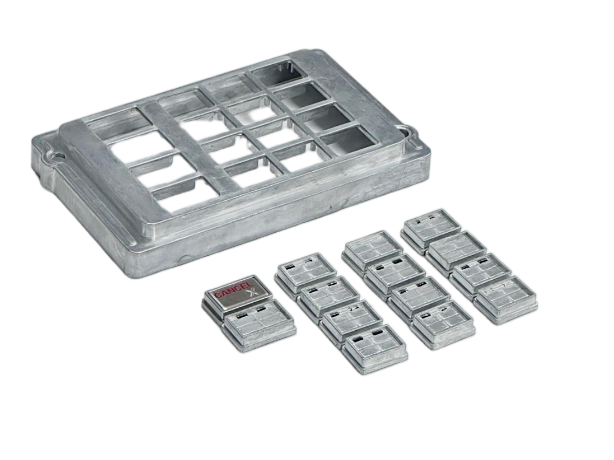
Secondary CNC
3- to 5-axis CNC milling, drilling & turning to refine cast components with ±0.02 mm accuracy.
- Tolerances as tight as ±0.01 mm
- Max workpiece size: 600 × 500 × 400 mm
- Lead times from 7 days

Surface Finishing
Comprehensive finishes—anodizing, powder coat, plating, polishing—to enhance durability and aesthetics.
- Salt spray resistance up to 500 h
- Ra ≤ 0.8 µm achievable
- Custom color & finish options
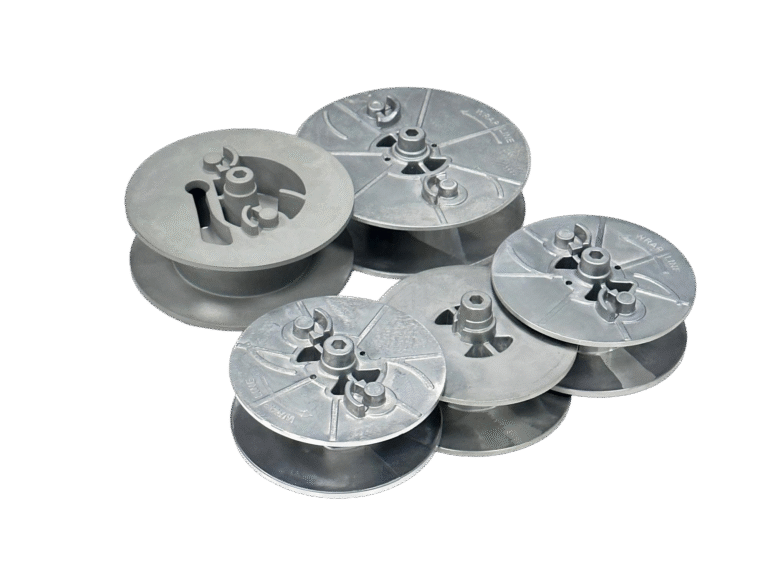
Rapid Prototyping
Quick-turn prototypes via 3D printing, silicone molding, and soft tooling to validate design fast.
- Sample in as little as 2 days
- Material options: PLA, ABS, urethane, silicone
- Low-volume runs up to 500 pcs
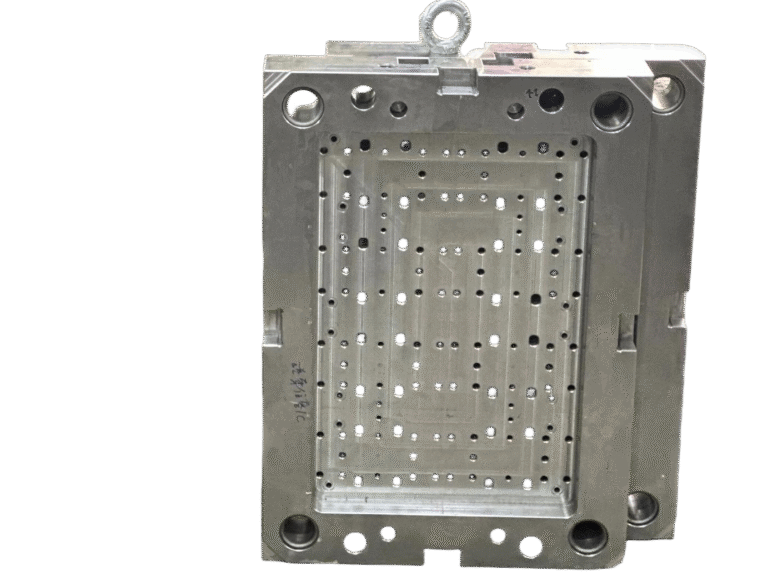
Die Casting Mold Making
Custom mold design and manufacture for aluminum & zinc die casting, ensuring precision and longevity.
- Mold life: up to 50,000 shots
- Cavity options: 1–4 cavities
- Lead times from 4–6 weeks
Total-Solution
Die Casting Services
CastMold owns ISO-certified facilities and partners with vetted workshops across Guangdong. Our integrated network delivers rapid aluminum and zinc die casting, precise CNC machining, and advanced surface finishing at scale—guaranteeing consistent quality and on-time delivery for your custom parts.

Die Casting Factory
- Established: 2010
- Anual Capacity: 10 million pcs
- Number of Machines: 7
- Location: Dongguan
Electroplating Factory
- Established: 2018
- Number of Plating Process Line:10
- Location: Dongguan
3D Printing Factory
- Established: 2018
- Number of Machines: 50
- Location: Dongguan
CNC Workshop
- Established: 2010
- Number of Machines: 10
- Location: Dongguan
Injection Molding Factory
- Established: 2010
- Anual Capacity: 100 million pcs
- Number of Machines:36
- Location: Huizhou
Painting Factory
- Established: 2014
- Number of Powder Coating Line: 5
- Location: Dongguan
Specialist
Industries
Unlock Potential
With the Right Metal
Discover our comprehensive selection of high-quality metals to suit your project needs and ensure optimal performance.
Quality Excellence in Every
Die Casting Component


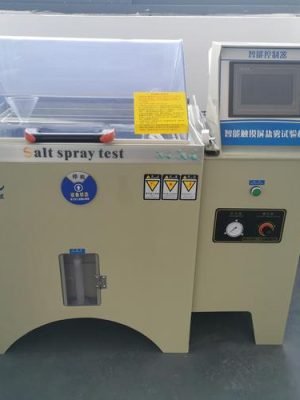
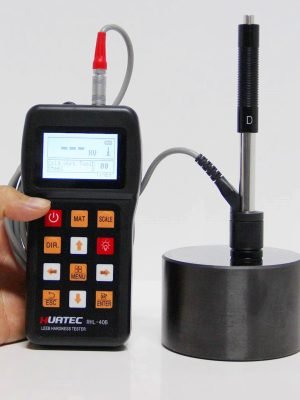
As a professional metal die casting manufacturer, CastMold embeds precision engineering into every production phase. Our ISO 9001:2015-certified quality system ensures strict compliance with global standards for durable.
Advanced Measurement, Guaranteed Accuracy
We deploy 10+ precision inspection tools, including CMM for 3D dimensional analysis, two-dimensional measuring instruments for surface flatness, and vernier calipers for micron-level tolerances. This multi-layered verification guarantees your castings meet exact specifications for weight, strength, and dimensional stability.
Rigorous Process Control Across All Stages
Our 10+ skilled quality inspectors implement phased checks:
- Pre-production: Mold integrity validation & material composition testing
- In-process: Real-time monitoring of pressure, temperature, and cycle parameters
- Final inspection: 100% assessment of surface finish, porosity, and mechanical properties
Comprehensive Documentation for Traceability
Clients receive detailed reports including:
- First Article Inspection (FAI) with GD&T analysis
- Material conformity certificates (e.g., ASTM, GB standards)
- Dimensional inspection sheets with CMM point-cloud data
Trusted by Global Partners
Through our ISO 9001:2015 framework, we deliver high-pressure die casting solutions with ≤0.05mm precision for automotive, electronics, and industrial applications.
HOW TO WORK WITH US
Some Number About Us
15 Years Experience
in Die Casting and Prototype Manufacturing.
The Lastest
Blog
Discover our latest insights on die casting innovations, industry trends, and expert tips—straight from the Castmold Blog’s newest post!
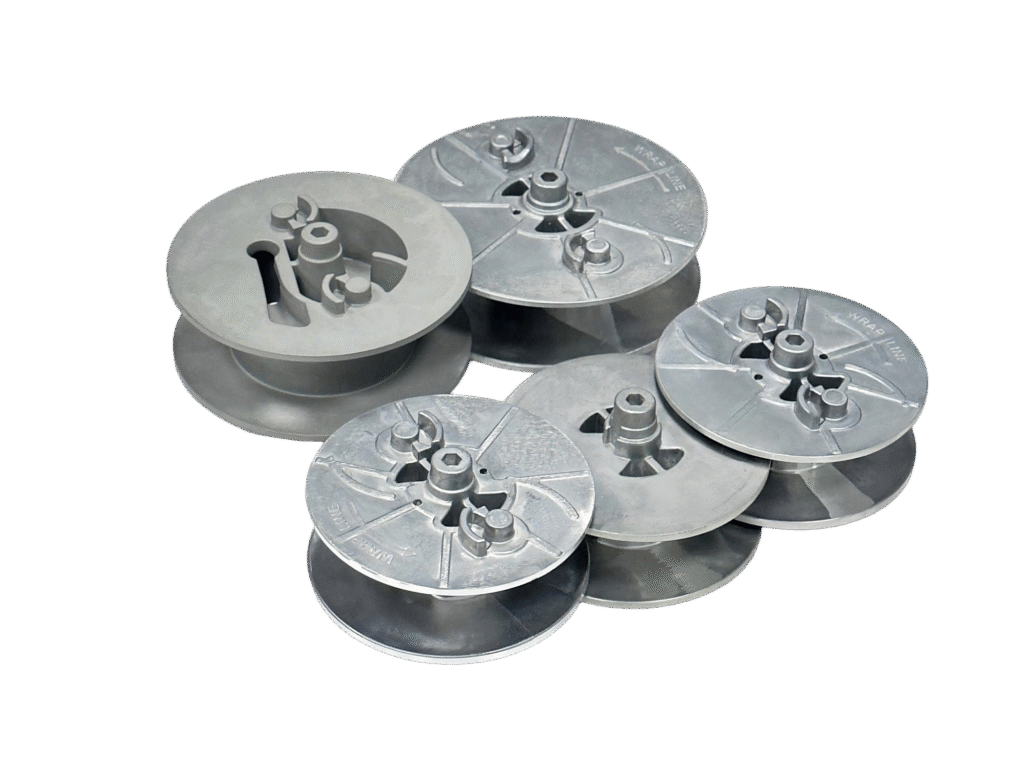
ADC12 Aluminum Alloy (A383/AC-46100): Properties, Composition, and When to Use It
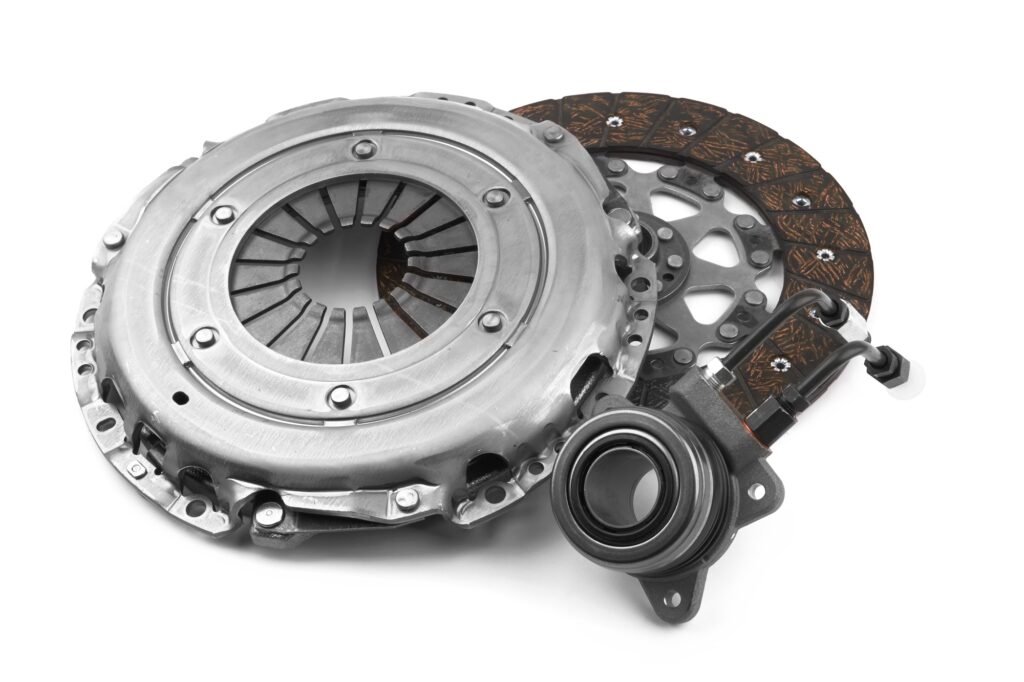
A380 Aluminum Alloy: Properties, Composition, and When to Use It
