Aluminum for casting provides a remarkable balance between lightweight design, high strength, and versatile applications. Widely used across automotive, aerospace, and electronics industries, selecting the right aluminum casting alloy is crucial to optimize both product performance and cost efficiency.
Aluminum for casting refers to specially formulated aluminum alloys designed for various casting methods—including die casting, permanent mold casting, and sand casting—to produce lightweight, durable, and precise parts ideal for numerous industrial applications.
Dive deeper into aluminum casting alloys, explore popular casting methods, and discover practical examples of aluminum casting’s role across different industries.
- What is Aluminum for Casting?
- Why Aluminum? Key Benefits for Casting
- Popular Aluminum Casting Alloys
- Common Aluminum Casting Processes
- Industrial Applications of Aluminum Casting
- Choosing the Right Aluminum Alloy for Your Project
- Industry Case Studies: Success Stories in Aluminum Casting
- Conclusion
- FAQ
- Crafting Excellence, Together
What is Aluminum for Casting?
Aluminum casting is a manufacturing process wherein molten aluminum alloy is introduced into a mold or die cavity to produce a solid, shaped part upon cooling and solidification. By definition, casting alloys are materials specifically engineered for the production of shape castings—products with complex geometrical forms that are often difficult or uneconomical to create using other manufacturing methods like subtractive machining from a solid billet. This near-net-shape production capability minimizes material waste and subsequent machining time, making it a cornerstone of modern industrial manufacturing
It is critical to distinguish between “cast aluminum” and “wrought aluminum.” While both originate from the same base element, their metallurgical properties and intended applications are fundamentally different. Wrought aluminum alloys are designed for mechanical forming processes such as rolling, extrusion, or forging, and typically have compositions that favor ductility and formability. In contrast, cast aluminum alloys are formulated with specific elements, most notably silicon (Si) and copper (Cu), to enhance properties crucial for the casting process itself. These additions improve the alloy’s fluidity in its molten state, reduce solidification shrinkage, and increase as-cast strength. For example, the higher silicon content in many casting alloys provides excellent flow characteristics, enabling the complete filling of intricate mold cavities, a property not required in wrought alloys. Consequently, cast aluminum parts possess a unique microstructure and mechanical property profile tailored for their specific method of creation and end-use application
Why Aluminum? Key Benefits for Casting
Aluminum is a premier choice for casting due to a powerful combination of beneficial properties. Its versatility allows it to meet a wide range of manufacturing demands, making it a cornerstone material in modern production.
- Lightweight with High Strength-to-Weight Ratio: The most significant advantage of aluminum is its low density, which is approximately 2.7 g/cm3, or roughly one-third that of steel or cast iron. This characteristic allows for the production of strong, durable components with minimal mass. In the automotive and aerospace industries, this translates directly to improved fuel efficiency, increased payload capacity, and enhanced performance dynamics.
- Excellent Corrosion Resistance: Aluminum naturally forms a thin, dense, and stable layer of aluminum oxide (Al2O3) on its surface when exposed to air. This passive oxide layer is self-healing and provides robust protection against many forms of corrosion, making aluminum castings ideal for applications in harsh environments, such as marine components or outdoor architectural fixtures, often without the need for additional protective coatings.
- Superior Thermal and Electrical Conductivity: Aluminum exhibits high thermal conductivity, allowing it to dissipate heat efficiently. This property is critical for applications such as engine components (cylinder heads, pistons) and electronic enclosures and heat sinks, where effective thermal management is essential for performance and reliability. Similarly, its excellent electrical conductivity makes it a choice material for electrical housings, connectors, and other components requiring good electrical performance.
- High Machinability: Compared to ferrous metals like steel and iron, aluminum alloys are significantly easier to machine. They are generally softer and chip more readily, which allows for faster machining cycle times, longer cutting tool life, and reduced labor costs associated with secondary finishing operations like deburring.
- Design Flexibility and Complexity: The casting process leverages the excellent fluidity of molten aluminum alloys to create parts with highly complex and intricate geometries that would be prohibitively expensive or technically impossible to produce through subtractive machining. This allows designers a high degree of creative freedom to integrate multiple functions into a single component, optimizing both performance and assembly efficiency.
- Recyclability: Aluminum is one of the most sustainable industrial materials due to its high recyclability. It can be recycled repeatedly without significant degradation of its mechanical properties. Critically, the recycling process consumes only about 5% of the energy required to produce primary aluminum from bauxite ore. This not only provides a significant environmental benefit by reducing energy consumption and greenhouse gas emissions but also contributes to a more cost-effective and circular manufacturing economy.
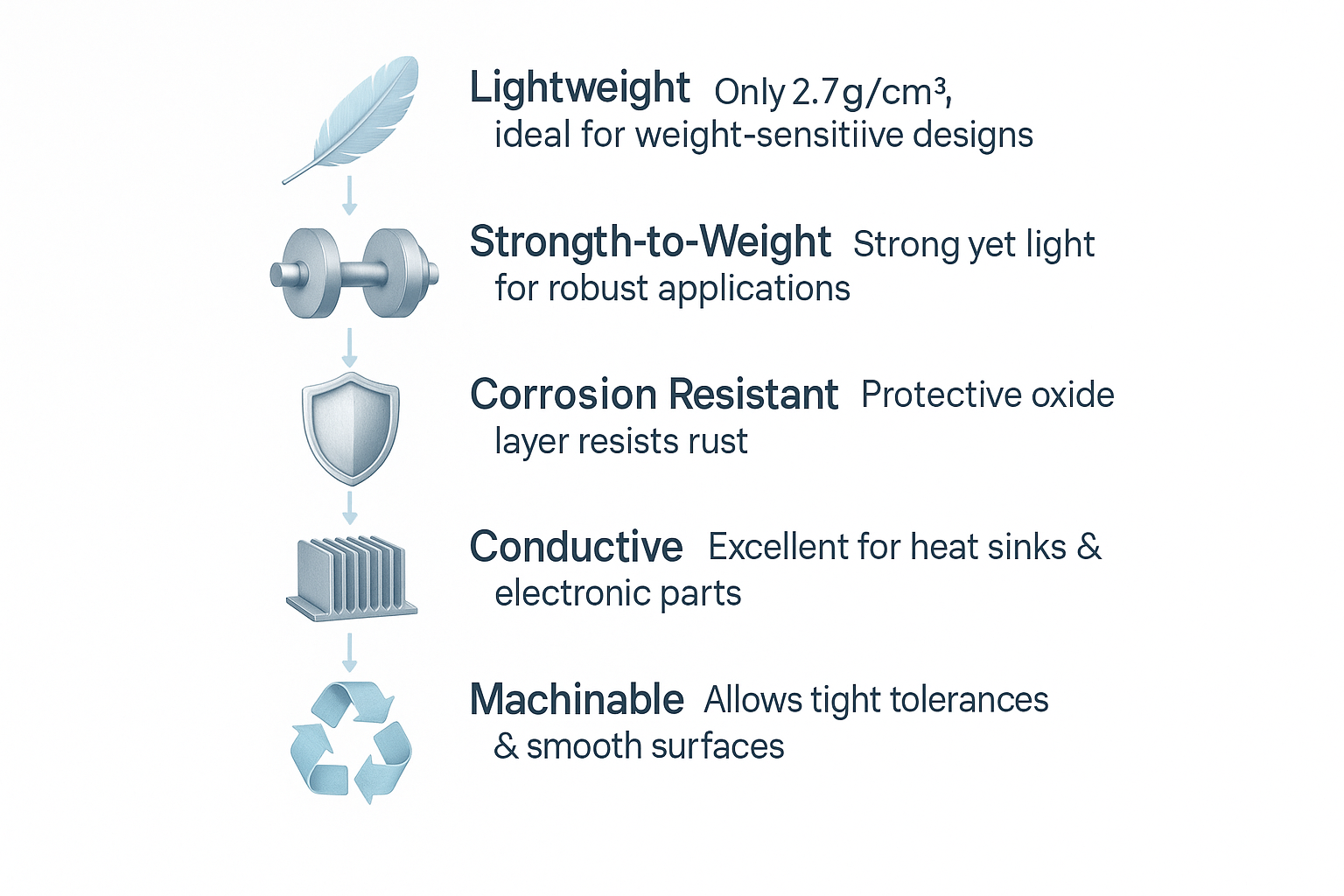
Popular Aluminum Casting Alloys
The performance of an aluminum casting is dictated by the specific alloy from which it is made. These alloys are carefully engineered with specific elemental additions to achieve a desired balance of properties. Understanding the relationship between an alloy’s composition, its resulting mechanical characteristics, and its ideal processing method is fundamental to successful component design and manufacturing.
- Alloy A380 (UNS A13800/A03800): The High-Pressure Die Casting Workhorse
- Alloy A356 (UNS A13560): The Premier Choice for High-Integrity Structural Parts
- Alloy ADC12 (JIS H 5302 / UNS A383): High Fluidity for Intricate Components
Comparative Metallurgical and Performance Data for Key Aluminum Casting Alloys
To facilitate direct comparison for material selection, the key properties of these primary casting alloys are summarized below. This data allows engineers and designers to evaluate the critical trade-offs between strength, castability, corrosion resistance, and post-processing requirements.
Property | A380 (UNS A13800) | A356-T6 (UNS A13560) | ADC12 (UNS A38300) |
Primary Alloying Elements | Si (7.5-9.5%), Cu (3-4%) | Si (6.5-7.5%), Mg (0.2-0.45%) | Si (9.6-12%), Cu (1.5-3.5%) |
Primary Casting Method | High-Pressure Die Casting | Permanent Mold, Sand | High-Pressure Die Casting |
Tensile Strength (MPa) | 317 – 324 | 228 – 310 | ~310 |
Yield Strength (MPa) | 159 – 160 | 165 – 228 | ~150 |
Elongation at Break (%) | 2.5 – 3.5 | 3 – 10 | ~3.5 |
Hardness (Brinell, HB) | ~80 | 70 – 105 | 75 – 85 |
Thermal Conductivity (W/m·K) | 96 – 109 | ~151 | ~96 |
Corrosion Resistance | Moderate | Excellent | Good |
Machinability | Excellent | Good | Good |
Weldability | Difficult | Excellent | Difficult |
Heat Treatable? | No | Yes (T5, T6) | No (Stress Relief Only) |
Recommended Use | High-volume die casting for engine components, transmission casings, and power tools. | Permanent mold casting for aircraft fittings, pump housings, and high-strength structural parts. | High-pressure die casting for complex, thin-walled electronic housings and automotive parts. |
The choice of aluminum casting alloy must align with the casting process. High-pressure die casting (HPDC) requires alloys like A380 with high fluidity for rapid filling but results in porosity, preventing heat treatment. In contrast, slower methods like permanent mold casting allow denser castings suitable for heat treatment, making alloys like A356 ideal. Matching alloy metallurgy to the process is crucial for optimal part performance.
Common Aluminum Casting Processes
The method used to cast an aluminum part is as critical as the alloy selection in determining the final component’s quality, cost, and performance characteristics. Each process offers a unique set of trade-offs regarding production speed, tooling investment, dimensional precision, and achievable mechanical properties.
High-Pressure Die Casting (HPDC): Precision at Scale
Process Overview:
HPDC uses a reusable two-part steel mold (die). Molten aluminum is injected from a cold chamber into the die under very high pressure (10–150 MPa). The metal cools quickly against the steel mold, and the finished part is ejected automatically, with cycle times of just seconds.
Advantages:
- High Speed & Volume: Ideal for mass production with low cost per part. Dies can produce hundreds of thousands of parts before replacement.
- Precision & Surface Finish: Produces parts with tight tolerances (±0.1 mm) and smooth surfaces (1–2.5 µm Ra), often eliminating further machining.
- Complex & Thin-Walled Parts: High pressure allows filling of intricate shapes and very thin walls (down to 1 mm), aiding lightweight design.
Limitations:
- High Initial Cost: Expensive and complex dies make it unsuitable for prototyping or low-volume runs.
- Porosity Risk: Fast injection can trap gases causing internal porosity, which affects strength and pressure tightness. Vacuum casting helps but doesn’t eliminate it.
- Material & Size Limits: Best for high-fluidity alloys like A380 and ADC12; large parts are limited by die size and clamping force.
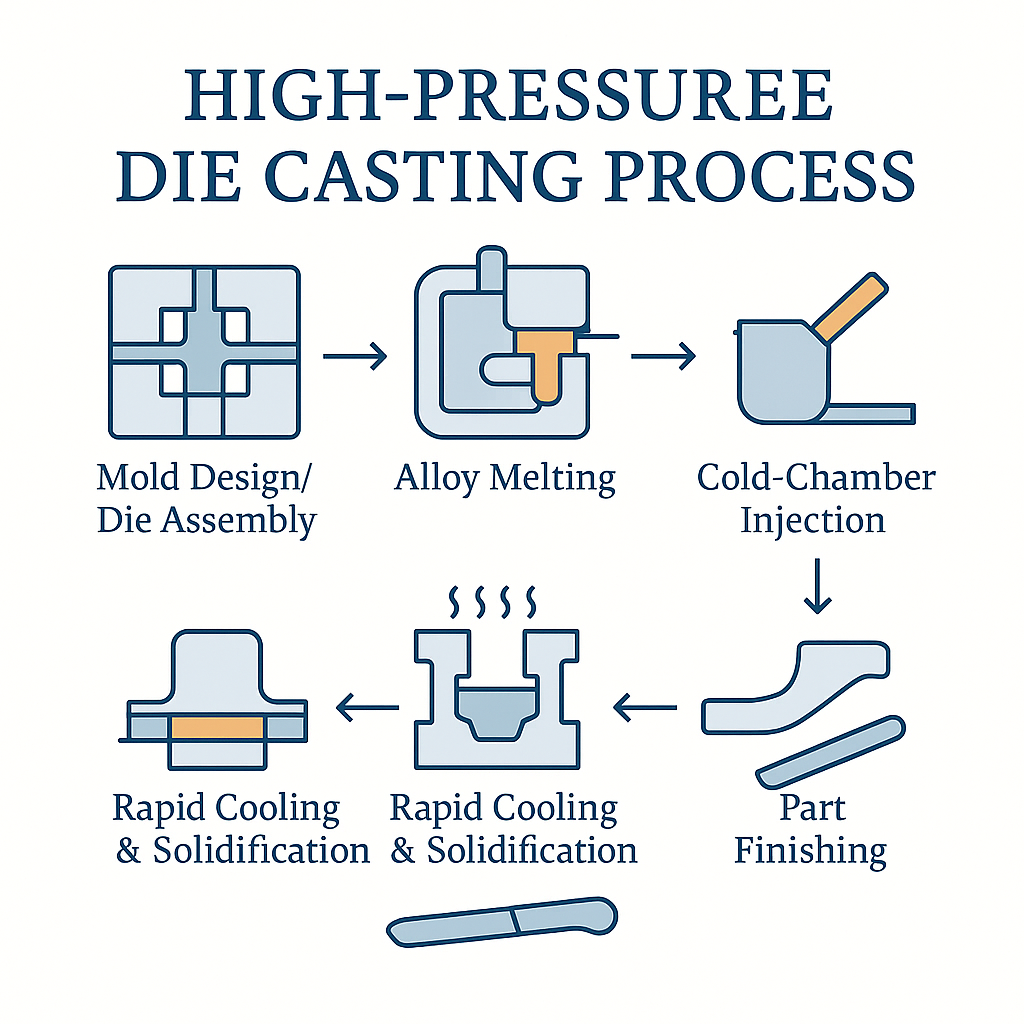
Sand Casting: Versatility and Low-Volume Economy
Process Overview:
Sand casting uses a reusable pattern to form a cavity in a special sand mixture. Molten aluminum is poured into this sand mold, allowed to solidify, then the sand mold is broken away to reveal the part. Sand cores enable complex internal shapes.
Advantages:
- Low Tooling Cost: Creating patterns is much cheaper than making steel dies, ideal for prototypes and low-volume or very large parts.
- Design & Size Flexibility: Can cast nearly any aluminum alloy and sizes from ounces to tons; cores allow intricate internal features.
- Fast Design Changes: New or modified patterns can be made quickly and inexpensively, speeding up development.
Limitations:
- Lower Accuracy: Sand molds lead to looser tolerances (±1.0 mm or more) compared to other methods.
- Rough Surface Finish: Cast parts have rough textures, usually requiring machining for smooth or mating surfaces.
- Slow Production: Each mold is single-use, making it unsuitable for high-volume mass production.
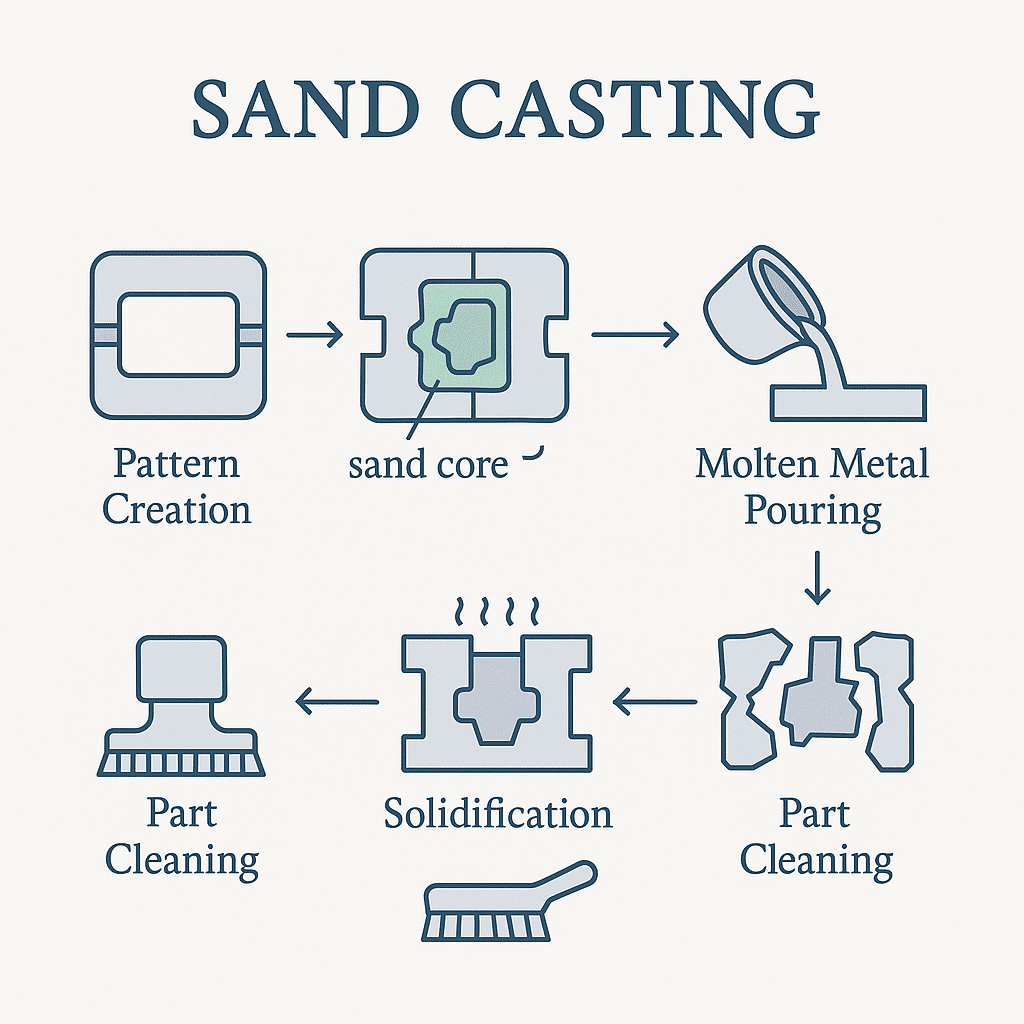
Permanent Mold Casting (Gravity Die Casting): The Quality-Cost Balance
Process Overview:
Permanent mold casting uses reusable iron or steel molds. Molten aluminum fills the mold by gravity rather than high pressure, often enhanced by tilt-pouring to reduce turbulence and air entrapment.
Advantages:
- Superior Mechanical Properties: Produces dense, fine-grained castings with low porosity, resulting in better strength, ductility, and pressure tightness than sand casting.
- Good Surface Finish & Accuracy: Smoother surfaces and tighter tolerances (±0.4 mm) reduce the need for machining.
- Cost-Effective for Medium Volumes: Tooling costs are higher than sand casting but lower than HPDC, ideal for thousands to tens of thousands of parts.
Limitations:
- Higher Tooling Cost than Sand Casting: Reusable metal molds require greater upfront investment.
- Slower Cycle Times than HPDC: Gravity fill and cooling take longer than high-pressure injection, limiting very high-volume use.
- Geometric Constraints: Metal dies restrict complex geometries with deep pockets or undercuts, unlike sand casting with cores.
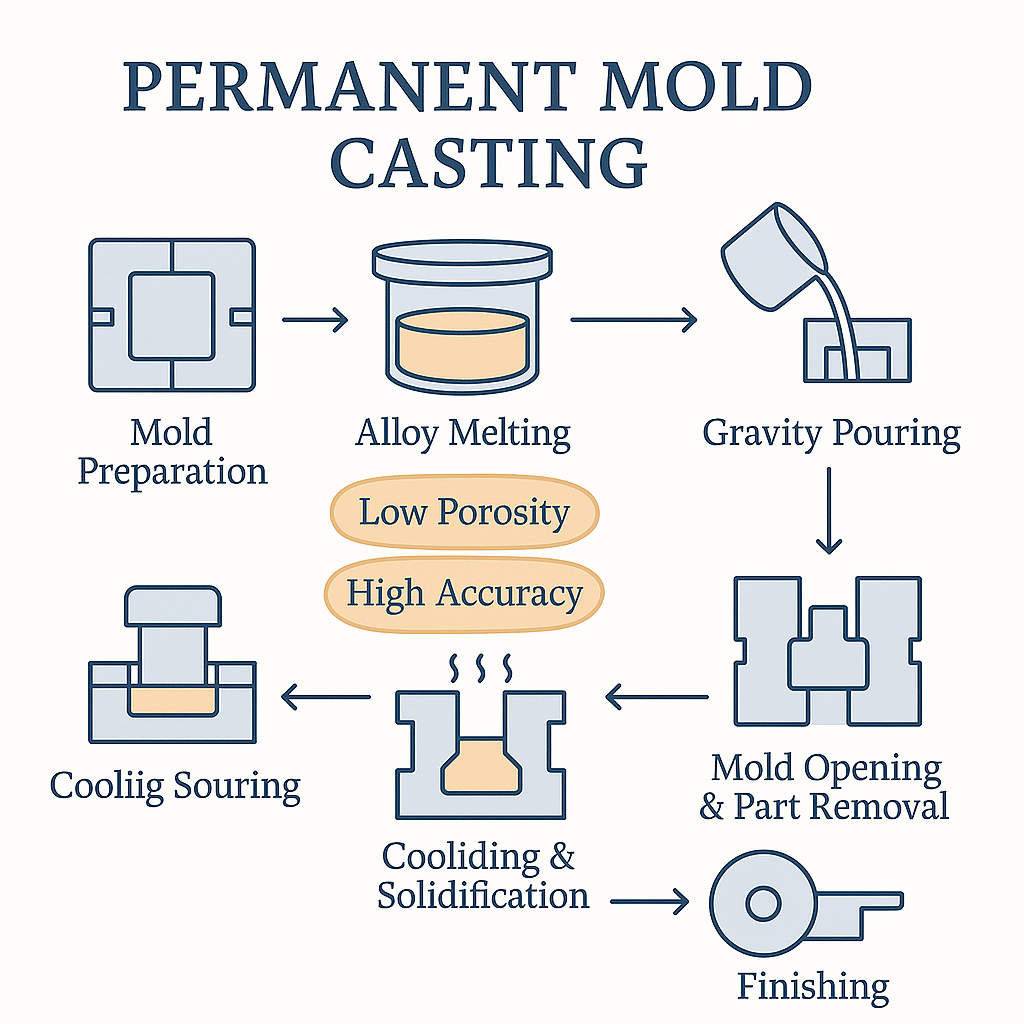
Multi-Criteria Process Selection Matrix
The selection of the optimal casting process is a multi-variable decision that depends on the specific technical and economic requirements of a project. The following matrix provides a comparative overview to guide this selection process.
Parameter | High-Pressure Die Casting (HPDC) | Sand Casting | Permanent Mold Casting |
Production Volume | High (10,000 – 1,000,000+) | Low to Medium (1 – 5,000) | Medium (1,000 – 50,000+) |
Tooling Cost | Very High | Very Low | Moderate |
Unit Cost (at volume) | Very Low | High | Moderate |
Dimensional Tolerance | Excellent (±0.1 mm) | Fair (±1.0 mm) | Good (±0.4 mm) |
Surface Finish (Ra) | Excellent (1-2.5 µm) | Poor (12-25 µm) | Good (2.5-7.5 µm) |
Part Complexity | High (thin walls, fine detail) | Very High (complex cores) | Moderate |
Typical Wall Thickness | Very Thin (≥1.0 mm) | Thick (≥3-5 mm) | Moderate (≥3.0 mm) |
Resulting Porosity | Can be High (mitigated by vacuum) | Low to Moderate | Very Low |
Mechanical Properties | Good | Fair to Good | Excellent |
Industrial Applications of Aluminum Casting
Aluminum castings are fundamental components across a wide range of industries due to aluminum’s exceptional combination of light weight, strength, corrosion resistance, and versatility. Below we explore the key sectors where aluminum casting plays a critical role and provide examples of typical applications.
The automotive sector has aggressively adopted aluminum castings to reduce vehicle weight, improve fuel efficiency, and extend electric vehicle (EV) range. Traditionally, engine blocks and cylinder heads were cast in iron; today, many are cast in aluminum with iron liners for weight savings. Aluminum die castings are also widely used for transmission housings, transfer cases, oil pans, wheel hubs, brake calipers, suspension components (control arms, knuckles), and structural parts like crossmembers.
- Example: The Ford F-150 utilizes an aluminum alloy body and numerous cast aluminum suspension and engine components to shed weight and enhance performance.
- Wheels: Low-pressure cast A356 aluminum wheels provide high strength after T6 heat treatment, significantly lighter than steel wheels.
- Electric Vehicles: Tesla’s innovative giga-casting process produces large, one-piece aluminum chassis sections, replacing multiple steel parts to simplify manufacturing and reduce weight.
High-pressure die casting is preferred for automotive parts due to its speed and precision, with alloys like A380 dominating applications such as motor mounts, alternator housings, and compressor bodies. The durability of aluminum under road-induced vibration and stress further establishes its value in this sector.
Aluminum casting is vital for electronics housings, heat dissipation, and electromagnetic interference (EMI) shielding.
- Applications: Die cast aluminum (often ADC12 alloy) is used for enclosures, junction boxes, connector bodies, telecom base station housings, and outdoor electronics due to its durability and corrosion resistance.
- Thermal Management: Heat sinks and heat exchangers are commonly aluminum castings, designed with fins and airflow passages for efficient cooling.
- Consumer Products: Projector housings, audio amplifier chassis, and camera frames sometimes use aluminum cast parts for light weight and structural integrity.
- Specialized Uses: Military and aerospace avionics often employ die-cast aluminum enclosures for vibration resistance and reliability, as in the F/A-18 fighter jet electronics housing, where a single casting replaced multiple components, reducing assembly complexity.
Aluminum’s non-magnetic and non-sparking properties make it especially suitable for electrical applications requiring safety and electromagnetic shielding.
Marine Industry
The marine environment is harsh, with saltwater rapidly corroding many metals. Aluminum’s natural oxide coating and lack of iron make it well-suited for marine use.
- Common Parts: Boat engine components, impellers, pump housings, valve bodies, propeller hubs, and structural hardware are frequently aluminum castings.
- Propellers: Smaller boat propellers are often cast aluminum with special coatings for corrosion resistance.
- Marine Engines: Aluminum engine blocks and cylinder heads with iron liners reduce boat weight. Personal watercraft engines and pump housings also rely on aluminum castings.
- Materials: Al-Mg based alloys like 518 are preferred for marine fittings due to excellent corrosion resistance. These parts are often anodized to further protect against saltwater damage.
- Examples: High-performance yachts use aluminum cast deck hardware and even hull sections for strong, corrosion-resistant one-piece structures.
Aluminum castings help reduce topweight and improve durability on the water, providing an ideal balance between weight and corrosion resistance.
Other Sectors
Aluminum castings are widespread in many additional industries:
- Industrial Machinery: Gear cases, bearing housings, levers, and other components benefit from aluminum’s lightweight and machinability.
- Medical Equipment: Cast aluminum bases and frames are used in imaging machines and hospital beds for durability and ease of handling.
- Consumer Goods: Cookware like die-cast aluminum pans offer quick, even heating.
- HVAC Systems: Aluminum cast fan impellers and blower housings reduce rotating mass and improve energy efficiency.
- Energy Sector: Aluminum cast parts appear in wind turbine gearboxes, oil and gas instrument housings, and more.
The ability to create complex shapes with good strength and corrosion resistance makes aluminum castings an enabling technology across diverse fields.
Choosing the Right Aluminum Alloy for Your Project
Selecting the best aluminum casting alloy depends on matching alloy properties to your part’s functional needs like strength, ductility, corrosion resistance, and manufacturing process.
Project Requirement | Recommended Alloy(s) & Reason |
---|---|
Thin walls or intricate details | ADC12 (A383): High silicon content provides excellent fluidity for sharp, fine features. Alternatives: A380, A383 with careful casting control. |
Maximum as-cast strength (no heat treatment) | A380 or ADC10: Strong alloys with added copper, tensile strength up to ~330 MPa. Ideal for structural, heavily loaded parts. |
High ductility or heat-treatable | A356 (A357): Can be heat treated (T5/T6) to boost strength (~275 MPa) while retaining ductility. Suitable for impact-resistant or weldable parts. |
Extreme corrosion resistance | Al-Mg alloys (A360, 518): Low copper content enhances corrosion resistance, ideal for marine or outdoor exposure. |
Pressure-tight or leak-proof castings | A413 (AlSi12) or A360: High silicon alloys with low porosity, suitable for hydraulic valves and sealed enclosures. |
High wear or abrasion resistance | A390: Hypereutectic alloy with silicon crystals for superior wear resistance, used in engine blocks and brake components. |
Industry Case Studies: Success Stories in Aluminum Casting
Understanding aluminum casting theory is valuable—but seeing its impact in real-world applications truly highlights its power. Below are three notable case studies demonstrating how the right alloy and casting process can revolutionize performance and manufacturing.
Case Study 1: 1903 Wright Flyer – Cast Aluminum Engine Crankcase
The Wright Brothers’ pioneering use of cast aluminum revolutionized aviation. To achieve flight, they needed an engine light enough to lift off. Traditional cast iron was too heavy, so they sand cast the engine’s crankcase from an aluminum-copper alloy (~8% Cu), weighing only 30 pounds—dramatically lighter than iron alternatives.
This lightweight crankcase enabled their 12 hp engine to weigh just 180 pounds total, achieving an unprecedented power-to-weight ratio that made powered flight possible. This early use of aluminum casting illustrated the metal’s unmatched strength-to-weight advantage and the importance of choosing the right alloy for performance—even at the cost of lower corrosion resistance, which was irrelevant for the short flight duration.
Today, aluminum cast crankcases remain standard in aircraft and many automotive engines, proving the lasting value of this innovation.
Case Study 2: Tesla Model Y – “Giga Casting” One-Piece Car Body
Tesla’s Giga Casting represents a modern breakthrough in automotive manufacturing. Instead of assembling dozens of stamped steel pieces for the underbody, Tesla partnered with Idra to create the world’s largest high-pressure die casting machine, capable of producing a single aluminum rear underbody casting (“megacast”).
This innovation reduced part count by about 70, cut manufacturing costs by ~40%, lowered weight, and improved chassis rigidity. The casting’s size posed challenges: typical heat treatments would cause distortion. Tesla solved this by developing a proprietary aluminum alloy that achieves high strength without T6 heat treatment, enabling large, thin-walled castings without warping.
Giga Casting showcases how combining new alloys with advanced casting processes can simplify complex assemblies, reduce costs, and push manufacturing limits. Tesla’s approach is influencing the whole automotive industry toward similar innovations.
Case Study 3: Converting a Steel Bracket Assembly to Aluminum Casting
Not all success stories are high-profile; many come from practical component redesigns. One example is an agricultural machinery bracket originally welded from multiple steel parts. By redesigning it as a single aluminum casting using A356 alloy and permanent mold casting, the weight dropped by 50%, assembly was vastly simplified (eliminating 12 welds and 5 parts), and overall costs fell by ~30%, despite slightly higher material costs.
The thicker sections and ribbing in the casting maintained strength while making the part easier to handle and improving machine performance. This case illustrates how aluminum casting’s design freedom and lightweight nature enable cost savings, weight reduction, and simplified manufacturing.
Conclusion
Choosing the appropriate aluminum casting alloy and process can dramatically enhance product quality, efficiency, and performance. Are you ready to leverage aluminum casting for your next project?
FAQ
For high-volume die casting, A380 is the workhorse alloy due to excellent castability and mechanical properties. Its variants like ADC12 are especially popular in Asia, making up over 90% of aluminum die cast parts in some regions. For sand and permanent mold casting, A356 is widely used, particularly when heat treatment is required.
Welding depends on the alloy: high-silicon die cast alloys like A380 are difficult to weld due to porosity and silicon content. Alloys like A356 are weld-friendly and often heat-treated (T5/T6) to increase strength. Die castings are generally used as-cast or with minimal heat treatment to avoid defects.
Aluminum doesn’t rust like iron but forms a protective oxide layer preventing further corrosion in neutral environments. However, aggressive environments (saltwater, acids) can cause pitting. Low-copper alloys (A356, A360) resist corrosion better. Protective coatings like anodizing enhance durability in harsh conditions.
Aluminum cast alloys typically have tensile strengths of 150–350 MPa, lower than steel’s 400–600+ MPa. However, aluminum’s density is about one-third of steel’s, giving it a high strength-to-weight ratio. Designs can compensate by increasing thickness, yielding lighter parts with adequate strength. Steel has higher stiffness and fatigue endurance but aluminum excels where weight savings matter.
Die casting uses reusable steel molds and injects molten aluminum at high pressure, producing precise parts with smooth surfaces and thin walls—ideal for high-volume, complex parts. Sand casting uses expendable sand molds, which are cheaper and flexible for large or custom parts but produce rougher surfaces, looser tolerances, and longer cycle times.