Surface Finishes
We Offer
Superior – quality surface finishing services are capable of significantly enhancing the aesthetics and functions of your parts, irrespective of the manufacturing process adopted. We are dedicated to delivering high – caliber metal, composites, and plastic finishing services, thereby facilitating you to actualize the prototype or part you have envisioned.
ROHS & REACH Compliance
ISO 9001:2015 Certified QMS
10+ Available Surface Treatment Processes
Multiple Verifications To Ensure Quality
Your Complete Solution To Aluminum Die Casting in China
At CASTMOLD, we deliver comprehensive, end-to-end manufacturing solutions under one roof.
After handling all phases of die casting and precision machining, we go the extra mile by offering expert surface finishing services. Our commitment extends until your project achieves flawless completion.
Our team provides both technical expertise and consultative guidance to help you select:
- The optimal surface treatment for your application
- The most effective quality control procedures
From functional and protective coatings to decorative finishes, we empower you to tailor every detail to perfection. Whether your priority is durability, aesthetics, or performance, we equip you with complete customization capabilities for outstanding results.
Why Surface Finishing is
Needed for Aluminum Die Castings?
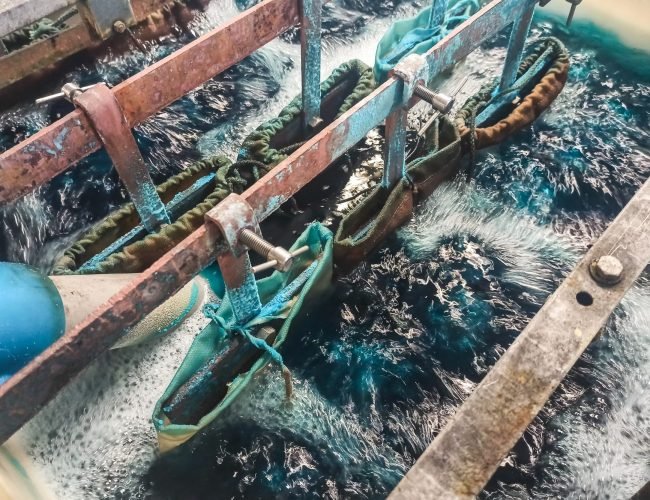
Surface treatment of aluminum die-cast components is essential to address inherent micro-defects (e.g., pores, shrinkage) from the casting process and enhance functional performance. The key benefits include:
-
Defect Sealing Treatments (e.g., passivation, shot blasting) seal subsurface microporosity (0.1-0.3mm dense layer) to prevent oxidation initiation.
-
Corrosion Resistance Anodizing or plating forms dense oxide films (e.g., Al₂O₃), increasing salt spray resistance by 2-5x for harsh environments.
-
Coating Adhesion Optimization Surface activation (e.g., phosphating, blasting) elevates roughness and chemical reactivity, boosting coating adhesion by 30%-50%.
-
Engineered Performance Hard anodizing achieves >600HV hardness; micro-arc oxidation creates ceramic coatings for wear/electrical resistance.
CASTMOLD – Precision Die Casting
& Surface Finishing Solutions
With advanced finishing techniques, we optimize corrosion resistance, wear protection, and cosmetic quality of aluminum die castings to meet your specifications.
-
Comprehensive Surface Finishing Solutions CASTMold offers a wide range of finishing options, including in-house Cleaning and Shot Blasting, as well as specialized partnerships for Liquid Painting, Powder Coating, Chromate Conversion Coating, Anodizing, Electroless Nickel Plating, Silk Screening, Pad Printing, and Laser Engraving.
-
Rigorous Quality Control From raw material inspection to final product testing, we enforce strict quality checks in our advanced laboratory to ensure precision and reliability.
-
ROHS & REACH Compliance Guaranteed All our surface-treated die-cast parts meet ROHS & REACH environmental standards, ensuring safety and regulatory compliance for your applications.
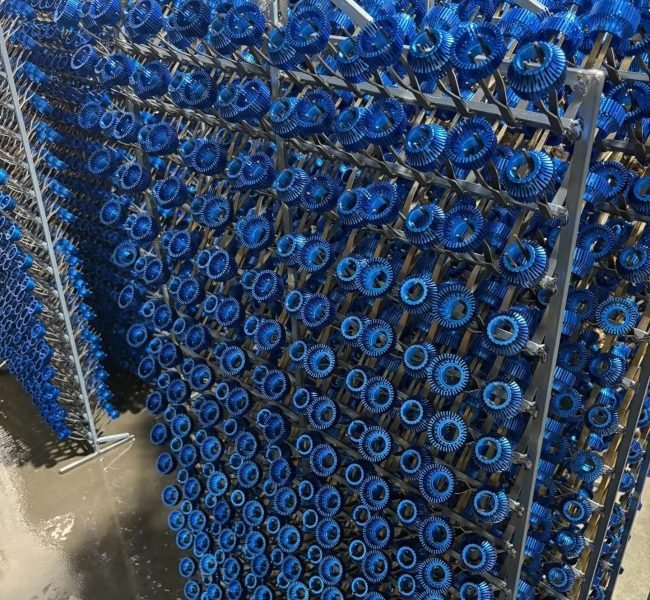
Anodizing-A High-Performance Surface Treatment
Anodizing is an electrochemical process that converts the aluminum surface into a durable, corrosion-resistant aluminum oxide layer. By immersing the part in an electrolytic solution and applying an electric current, we create a fully integrated coating that bonds molecularly with the substrate—unlike paint, which can chip or peel. The result is a hard, wear-resistant finish that enhances both performance and longevity.
-
Enhanced Corrosion Resistance Forms a dense aluminum oxide layer (Al₂O₃) that resists corrosion from acids, alkalis, and salt spray.
-
Increased Wear Resistance Surface hardness reaches 300-600HV, extending component lifespan.
-
Customizable Aesthetics Electrolytic coloring enables diverse color and gloss finishes.
-
Eco-friendly Compatibility The process is free of heavy metal pollution and compatible with subsequent coating or bonding processes.
Powder Coating – Electrostatic Spray Process
A dry powder (thermoplastic or thermoset polymer) is electrostatically applied to grounded metal, eliminating solvents for thicker, tougher coatings. Positively charged powder adheres to the negatively charged part, then cures at ~200°C—thermosets crosslink for strength, thermoplastics melt into a solid finish.
-
Zero solvent emissions & eco-friendly VOC-free process complies with EU RoHS standards, reducing occupational hazards and environmental pollution.
-
Thicker coatings without sagging/dripping Achieve 80-120μm thickness in one step via electrostatic adhesion, eliminating rework and accelerating production.
-
High hardness (150-350HV) & corrosion resistance 150-350HV hardness and 48+ hrs salt spray resistance (ASTM B117) ensure long-term reliability.
-
Wide color gamut & customizable finishes 200+ RAL colors, gloss/texture options (e.g., metallic, wrinkled) meet diverse design specifications.
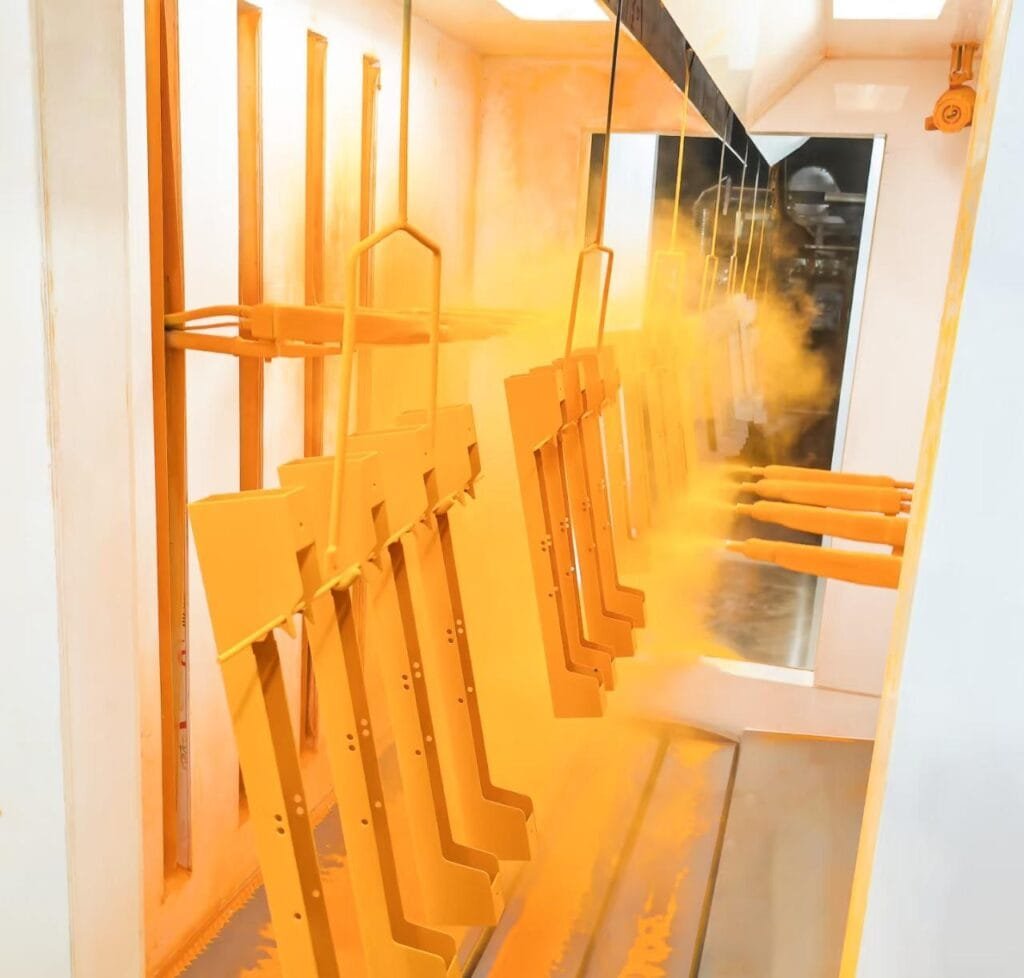
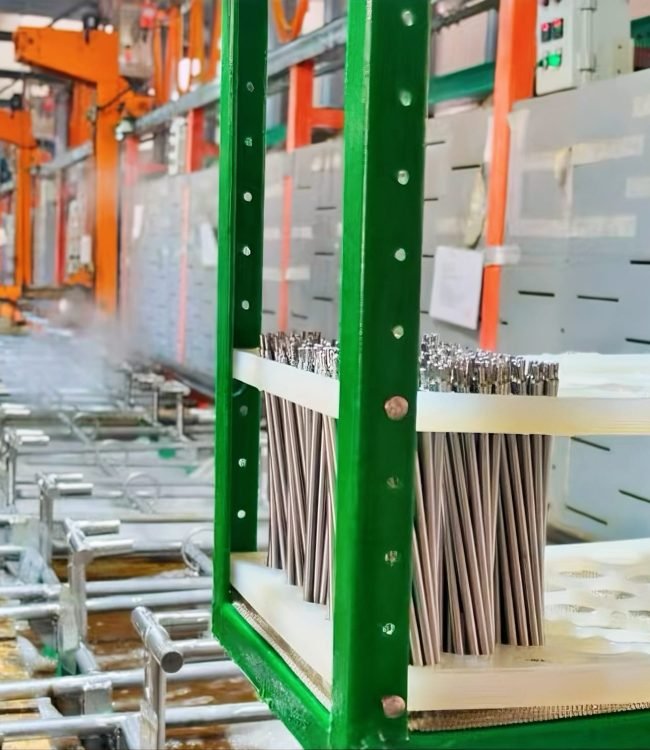
Electroless Nickel Plating – Autocatalytic Deposition Process
Electroless nickel plating (ENP or NiP) is a chemical process that deposits a nickel-phosphorus alloy onto metal surfaces without the use of electricity. Unlike electroplating, ENP relies on an autocatalytic chemical reaction, resulting in a uniform coating thickness—even on complex geometries—due to the absence of electric field variations. This method offers superior wear and corrosion resistance, though it requires longer processing times.
-
Uniform Coating Thickness No reliance on electric current enables uniform nickel-phosphorus alloy deposition, even on complex geometries
-
No Electrical Requirement A purely chemical reaction (non-electrolytic) eliminates electric field interference, ensuring consistent deposition
-
Customizable Alloy Composition Adjustable properties (e.g., brightness, magnetism, corrosion resistance) through controlled phosphorus content (e.g., 5-9% medium phosphorus)
-
Wear and Corrosion Resistance Medium phosphorus coatings offer moderate corrosion resistance, while increased thickness (e.g., ≥0.0002") enhances wear resistance and durability
E-Coating - High-Quality Coating
E-coating is a surface finishing process where a pre-treated conductive substrate is immersed in a water-based bath containing epoxy or paint. Under an applied electric field, cationic resin particles uniformly deposit onto the substrate via electrophoretic migration, forming a dense and consistent film. This method delivers exceptional corrosion resistance (ideal for moisture-prone environments), full coverage of complex geometries (e.g., tight cavities), and superior adhesion with resistance to salt spray and acids.
-
High Environmental Friendliness E-coating uses water-based coatings with minimal VOC emissions, aligning with eco-friendly production standards.
-
Superior Uniform Coverage Electrically driven deposition ensures even coverage on complex geometries (e.g., cavities, edges) with no blind spots.
-
Enhanced Corrosion Resistance Dense organic layers isolate metal substrates from corrosive elements (e.g., moisture, salt spray) for long-term protection.
-
Compatibility with Automated Production Ideal for high-volume automated lines with fast processing, low cost, and consistent quality output.
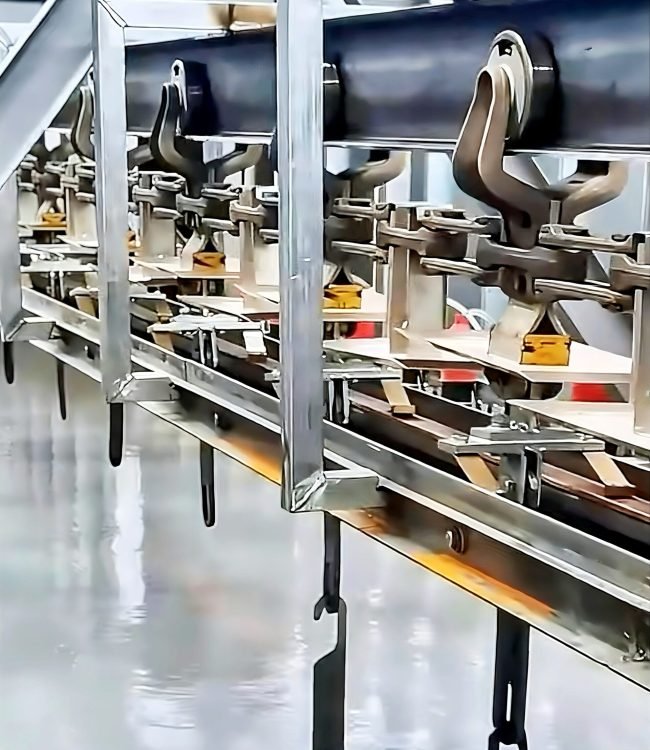
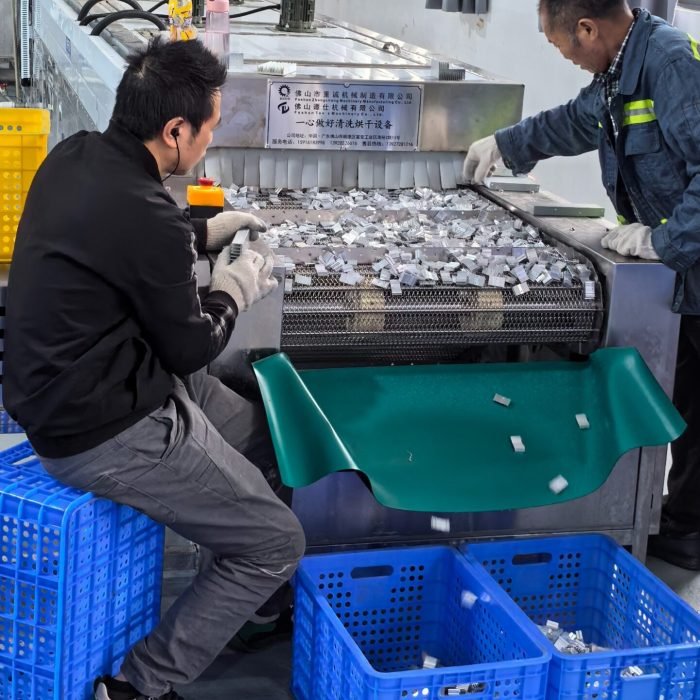
Passivation Process
Passivation is a non-electrolytic chemical process that forms a dense oxide layer on aluminum alloy surfaces, enhancing corrosion resistance and oxidation resistance while preserving the original appearance and dimensional stability. The process includes degreasing, activation, passivation, and post-treatment steps, suitable for complex geometries
-
Eco-Friendly & Low Consumption Uses chromium-free or low-toxicity solutions, minimizing wastewater impact and complying with RoHS.
-
High Efficiency & Cost-Effective Operates at ambient temperature (20-40℃) with short cycle time (3-10 mins), requiring minimal equipment and energy, ideal for mass production
-
Uniform Coverage Self-limiting reaction ensures consistent film growth on complex geometries, including internal cavities.
-
Broad Compatibility Compatible with various alloys (e.g., ADC12, A380); the passive layer (50-200mg/m²) provides an ideal base for subsequent coatings like painting or electrophoresis
Electroplating Process
Electroplating deposits metal coatings (e.g., nickel, chromium) on aluminum die-casting surfaces via electrolysis, improving corrosion resistance, conductivity, and aesthetics, with pre-treatments (e.g., zinc immersion) to enhance adhesion
-
Process Adaptability Special pre-treatments (zinc immersion/electroless nickel) overcome aluminum's reactivity for reliable coating adhesion
-
Multi-Functional Versatile metal options (copper, silver, gold) enable tailored properties like conductivity or EMI shielding
-
Enhanced Aesthetics Mirror, matte, or antique finishes meet premium aesthetic demands in luxury and electronics
-
Eco-Friendly Solutions Cyanide-free processes minimize toxic waste, aligning with RoHS and environmental standards
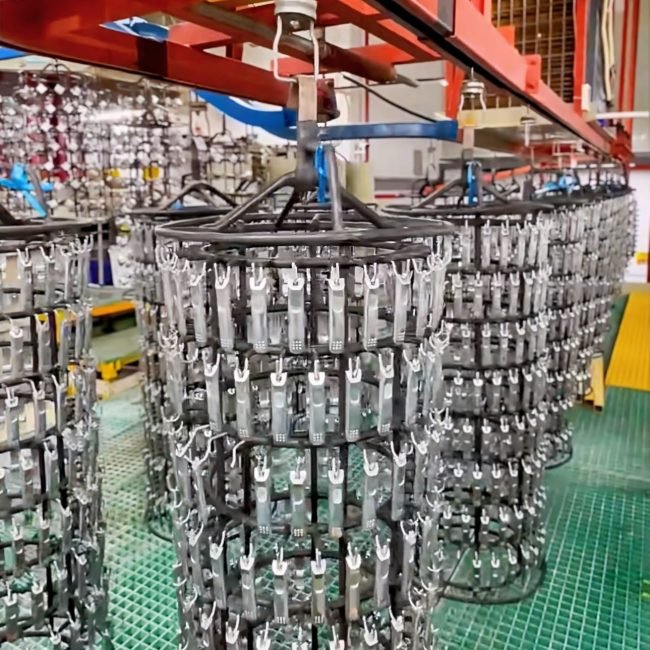
Proven Expertise in Die Casting Surface Finishing
With 1,000+ precision die casting parts treated and delivered to 500+ clients worldwide, CASTMOLD has established itself as a trusted partner for high-quality surface solutions.
Our Experience Includes:
✔ Diverse Industry Applications – Automotive, aerospace, electronics, and industrial components
✔ Advanced Finishing Techniques – Anodizing, powder coating, plating, polishing, and more
✔ Global Clientele – Serving manufacturers across North America, Europe, and Asia
We ensure durability, aesthetics, and compliance with industry standards—partner with us for reliable, high-performance surface treatments.
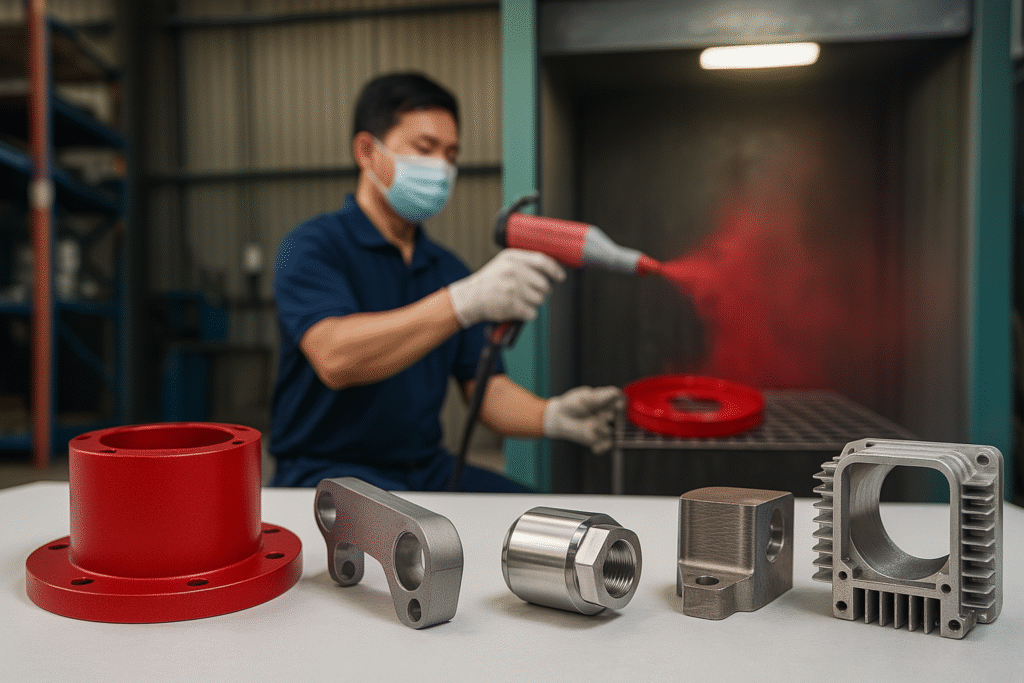
FAQs
Die casting is a metal casting process where molten metal is forced under high pressure into a reusable steel mold cavity6. The mold, composed of two hardened dies, operates similarly to an injection mold, enabling high-volume production of small to medium-sized parts with excellent surface finish and dimensional consistency6. Key steps include melting the metal (commonly aluminum, zinc, or magnesium alloys64), injecting it into the die under high pressure, and cooling to form the final part6.
This process is widely used in automotive manufacturing for lightweight, complex components like engine blocks and structural frames41. For example, Tesla employs 6,000-ton gigacasting machines for front and rear underbody parts1, while AITO M9 uses a 9,000-ton press for rear sections1. Advantages include cost-effectiveness (due to reusable dies), rapid production cycles, and high structural integrity46.
1. Wall Thickness
Maintain uniformity (2.5–4 mm for aluminum alloys), avoid thick sections (>6 mm) to prevent gas porosity; use ribs/gussets instead of localized thickening, and ensure gradual transitions to reduce stress.
2. Draft Angle
Minimum 0.25°–1.5° (1°–3° for deep cavities or textured surfaces); align draft direction with mold opening to avoid undercuts.
3. Fillets
Internal radii ≥0.5 mm (recommended: 1/2 to full wall thickness) to enhance strength and fill; round external edges for easier mold maintenance.
4. Gating System
Place gates near thick sections for laminar flow to minimize air entrapment; tapered runners and small gates require high pressure but simplify trimming.
5. Venting
Add 0.1–0.15 mm deep vent slots along the parting line; critical components use vacuum-assisted systems with dual vents to reduce porosity.
6. Geometric Simplification
Eliminate undercuts, optimize parting lines for minimal complexity, and adopt symmetry to reduce thermal distortion and improve mold stability.
The tolerances for die casting vary depending on the process and part dimensions. For pressure diecasting, the flatness tolerance is typically 0.2 mm for dimensions up to 75 mm, with an additional 0.075 mm added per 25 mm increase in size4. These values reflect standard production practices optimized for cost-effectiveness. Higher precision may require specialized processes or additional post-casting machining. For example, surface roughness in high-pressure die casting can achieve Ra 1.6–6.3 μm under optimal conditions1, though dimensional tolerances remain primarily governed by the casting size and material flow characteristics. Designers should specify tighter tolerances only where functionally necessary, as achieving them often increases production complexity.
Our design team utilizes specialized software for product development and mold flow analysis, ensuring designs meet production requirements. Through pre-production simulations, we optimize processes to reduce trial runs and improve yield.
We are well-versed in PPAP processes and can prepare complete Production Part Approval documentation, guiding clients through the review procedures.
Our ISO 9001:2015 certified quality management system ensures full-process monitoring from raw materials to finished products, including first-article inspection, in-process checks, and final inspection.
We implement annual improvement plans, regularly optimizing processes and efficiency through customer feedback and production data analysis.
We offer flexible lead times of 2-10 weeks, tailored to design complexity and client requirements. Through parallel design confirmation and modular manufacturing solutions, standard projects can be delivered in as fast as 2 weeks, with complex projects completed within 10 weeks maximum.